Nanoparticle Tracing during Laser Powder Bed Fusion of Oxide Dispersion Strengthened Steels
2021/07/08
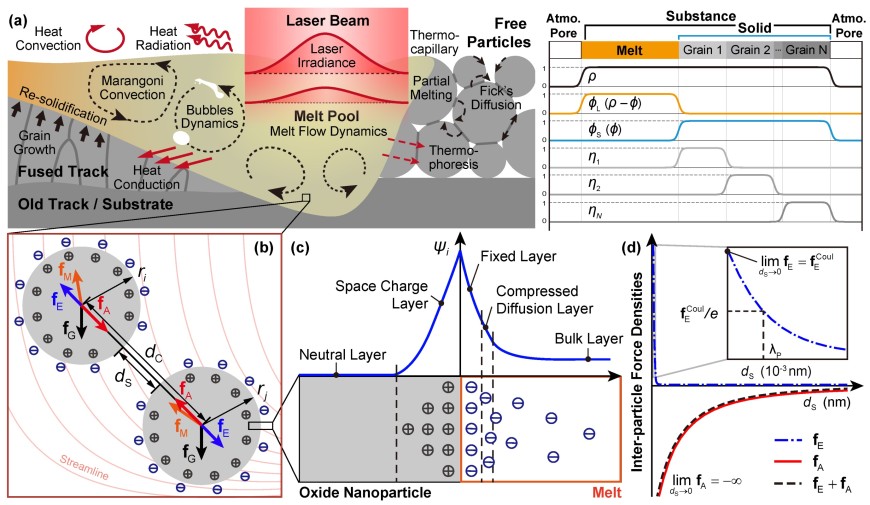
Y. Yang, C. Doñate-Buendía, T. David Oyedeji, B. Gökce, B.-X. Xu
Materials, 14, 3463, (2021).
The control of nanoparticle agglomeration during the fabrication of oxide dispersion strengthened steels is a key factor in maximizing their mechanical and high temperature reinforcement properties. However, the characterization of the nanoparticle evolution during processing represents a challenge due to the lack of experimental methodologies that allow in situ evaluation during laser powder bed fusion (LPBF) of nanoparticle-additivated steel powders. To address this problem, a simulation scheme is proposed to trace the drift and the interactions of the nanoparticles in the melt pool by joint heat-melt-microstructure–coupled phase-field simulation with nanoparticle kinematics. Van der Waals attraction and electrostatic repulsion with screened-Coulomb potential are explicitly employed to model the interactions with assumptions made based on reported experimental evidence. Numerical simulations have been conducted for LPBF of oxide nanoparticle-additivated PM2000 powder considering various factors, including the nanoparticle composition and size distribution. The obtained results provide a statistical and graphical demonstration of the temporal and spatial variations of the traced nanoparticles, showing ∼55% of the nanoparticles within the generated grains, and a smaller fraction of ∼30% in the pores, ∼13% on the surface, and ∼2% on the grain boundaries. To prove the methodology and compare it with experimental observations, the simulations are performed for LPBF of a 0.005 wt % yttrium oxide nanoparticle-additivated PM2000 powder and the final degree of nanoparticle agglomeration and distribution are analyzed with respect to a series of geometric and material parameters.
DOI: 10.3390/ma14133463
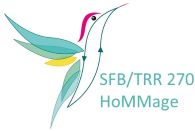