Face masks made using 3D printers
2020/04/23 by sip/cst
Face masks for the treatment of corona patients are currently in very short supply, which is why the Hessian Ministry of Economics recently called on businesses to support them in the procurement or production of equipment to protect against infection. This appeal was answered by various facilities at TU Darmstadt and protective masks are now being produced using frame components, holding straps and plastic film. The frame components are being produced with the aid of a 3D printer. The assembled masks cover the mouth, nose and eyes.
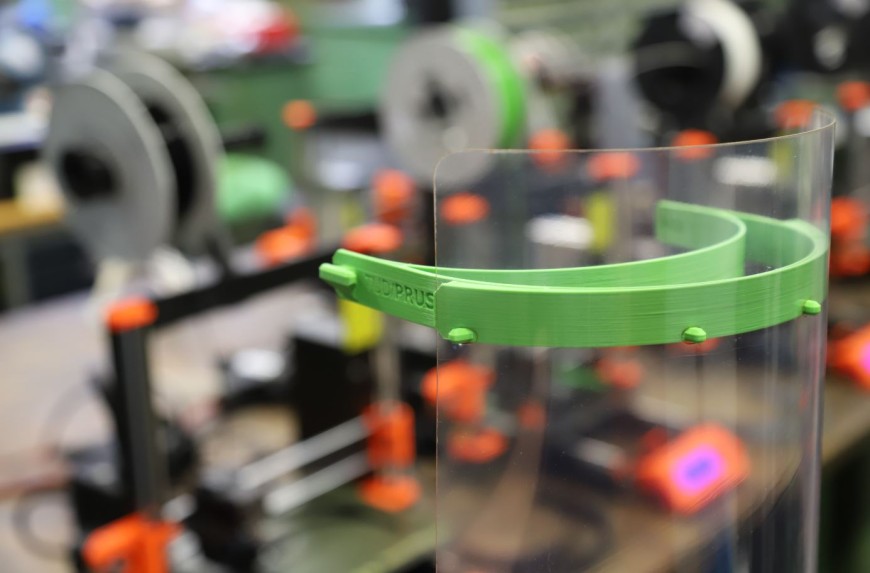
Department of Civil and Environmental Engineering
Departments of Architecture and Mechanical Engineering
Peter Maier (Head of the Model Workshop in the Department of Architecture) and Mirko Feick (Head of the Mechanical Workshop for Production Management, Technology and Machine Tools ()/Institute for Production Engineering and Forming Machines ( PTW) in the Department of Mechanical Engineering) have also started production of disposable, full-face masks. For this aid project, the company Paul Auer GmbH based in Mannheim provided 300 metres of plastic film at short notice and free of charge for the production 900 face visors. Since then, 16 printers at the two departments have been producing visor frames, while the team are busy cutting the film and assembling the finished masks by hand. PtU
The team then also went one step further and improved the model: Thanks to a clever geometrical adjustment to the plastic frame by Peter Maier and the technological expertise of two doctoral students in the Department of Mechanical Engineering Johannes Geis (Institute for Product Development and Machine Elements ()) and Holger Merschroth (Institute PTW), it was possible to improve the original two-piece design of the plastic frame for the visor and produce it in one single piece. This has reduced the number of steps required to assemble the masks, shortened the production time by 25 percent and achieved a significant improvement in productivity. Using the 3D printers in the Departments of Architecture and Mechanical Engineering, 50 reusable, full-face masks can currently be produced per day. The masks are then supplied to hospitals. pmd
Institute of Computer Integrated Design (Department of Mechanical Engineering)
The (DiK, Department of Mechanical Engineering), headed by Professor Dr. Reiner Anderl, is also producing full-face masks. The institute is providing the 3D printers and materials required to print the frames, which are then passed on to the FabLab at TU Darmstadt. The visors are then prepared and assembled there. Thanks to this cooperation, it has already been possible to produce and distribute 150 full-face masks. The first batch were taken by nursing homes and hospitals in Darmstadt. Institute of Computer Integrated Design
Other networks of specialist fields within the Department of Mechanical Engineering are currently being developed in this context to bundle together the available resources, coordination capabilities and distribution channels.
Focus "Fighting Corona"
Researchers, students and employees at the university are responding to the current corona crisis in a variety of ways. The focus provides an up-to-date overview of the numerous aid initiatives and projects in research, teaching and transfer.